The Art of Breguet: An Engineer’s View at Craftsmanship
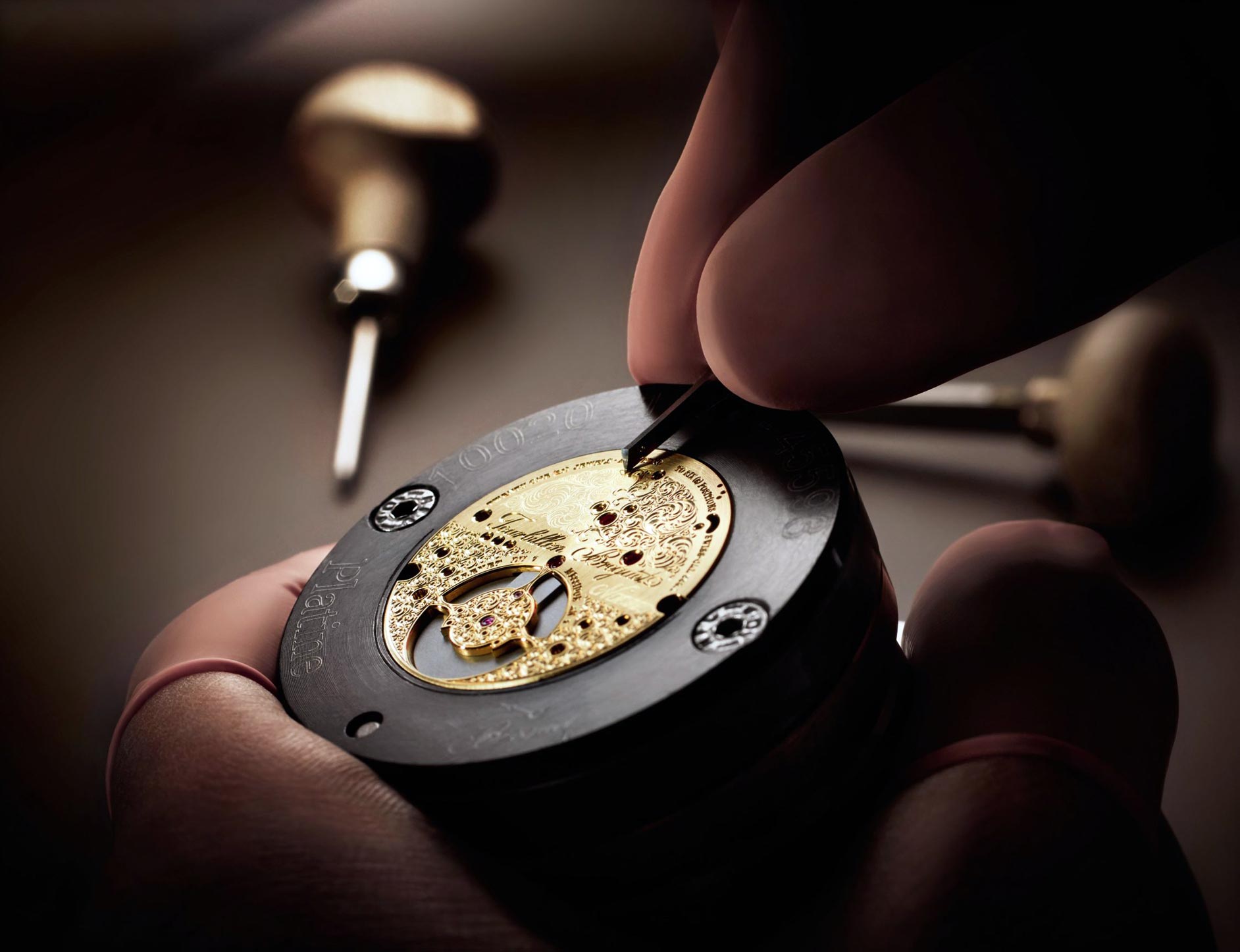
At Breguet, the artisanal crafts are not just an exercise in watchmaking mechanics but they represent the very essence of the House of Breguet; which has always valued aesthetics and the artisan technique of the craftsman in equality with engineering and accuracy. Retaining these skills is so important to Breguet that the manufacture puts a great deal of energy into ensuring that the crafts survive by training their artisans. In this article, we discover four of the main handcrafted techniques used by Breguet to ensure each watch is a uniquely crafted piece of art and masterpiece in precision engineering.
Guillochage (engine turning)
Completed by hand, the art of Guillochage is a true signature element of the House of Breguet. Used in watchmaking for the first time in 1786 by Abraham-Louis Breguet, guilloche design has never been more prominent at the Breguet manufacture. At the Breguet manufacture, a number of antique hand operated lathes are in use today, continuing to push the technique to new heights, as well continuing the tradition by building approximately thirty new engine-turning lathes. Based on original concepts, they were given a state-of-the-art update in terms of ergonomics, lighting, optics, and precision. The workshop thus became one of the most important in the entire watchmaking industry, as artisans craft a variety of geometric patterns.
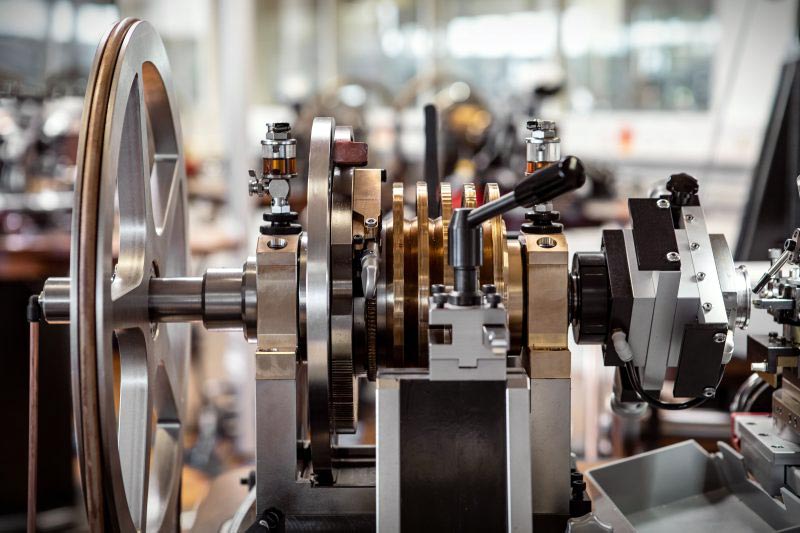
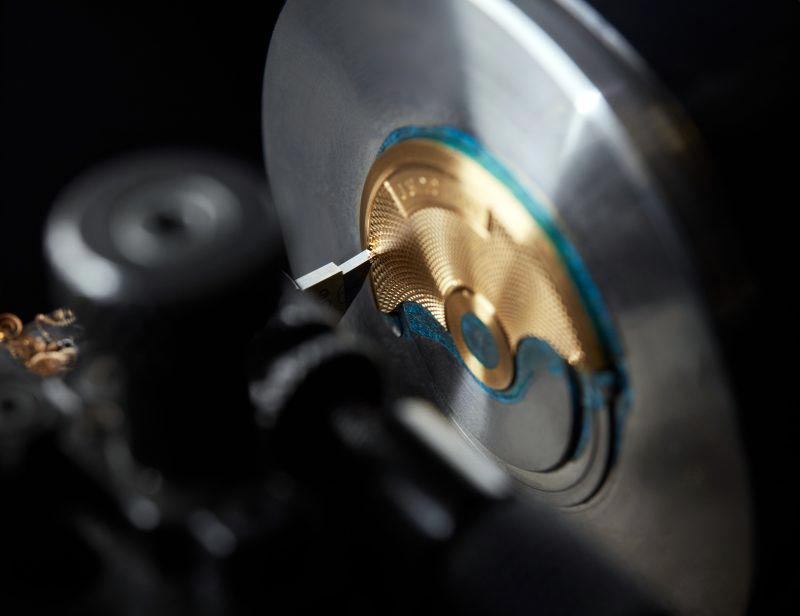
Guillochage engine-turning lathe at the Breguet manufacture. An example of the intricate and highly skilled guilloche design
Hand Engraving (Chasing)
A craft endured throughout the ages to become part of Breguet’s identity today, the artisans responsible for this craft have been trained predominantly in-house, and have an extraordinary capacity for respecting an “artistic grammar” unique to the House of Breguet, while preserving their own particular aesthetic vocabulary – the main asset of any artisanal work. Except for the use of binoculars, the tools and methods have stayed the same for hundreds of years, responsible for creating finely detailed images on the main plates, bridges and open-worked winding rotors. Known as “taille douce” or soft carving, is exceedingly difficult to master and increasingly rare today. The technique involves creating designs using a series of fine lines, applied with a constant and controlled amount of pressure.

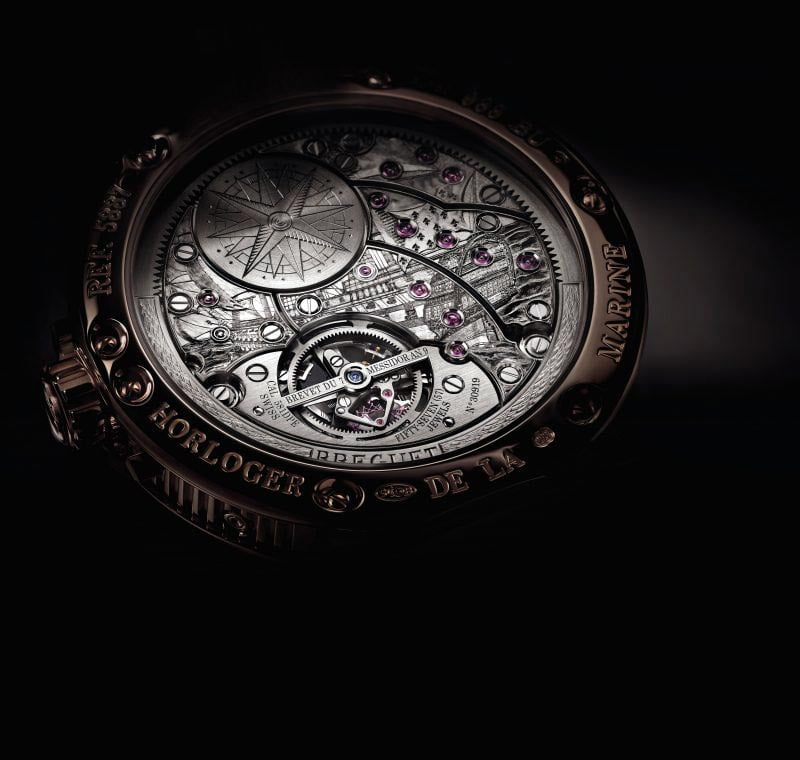
Taille Douce engraving on the Classique 3358 and the Marine 5887 Equation of Time
Anglage (Chamfering or Bevelling)
Requiring immense dexterity, anglage is a technique involving filing the sharp edges from various components, thus creating a chamfer – or bevel – at a 45-degree angle, whose width must be constant, and its angles perfectly parallel. The polishing process must then ensure that the piece has a uniform reflection, without kinks or facets. Finally, and this is the true hallmark of a master, the inner corners must reveal no less than a sharp and clean line where the two bevels meet. Performed by hand the finish is achieved by using hand files in the first stages before various grades of diamond paste is applied for the final finish. Not only is there no machine that can produce such a result, but training programs for this craft have also disappeared. The anglage workshop at Breguet, has been created to keep this art alive and demonstrates the extreme attention paid to the quality and finish of Breguet movements.
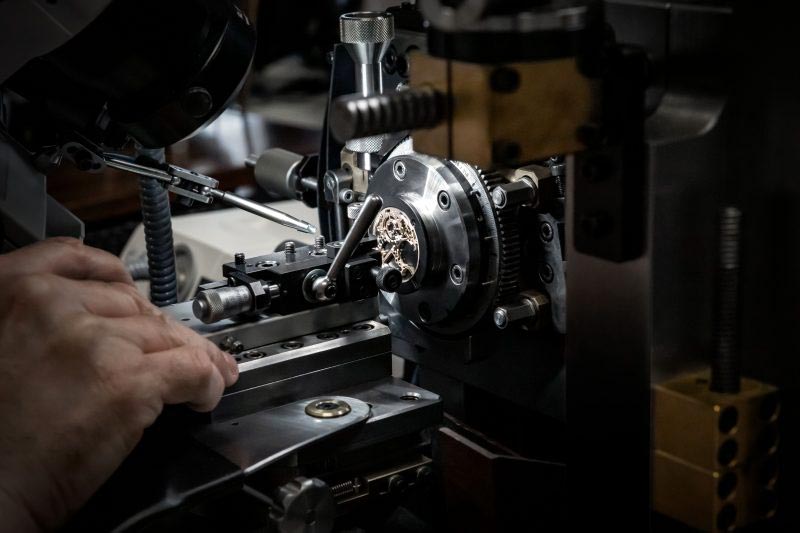
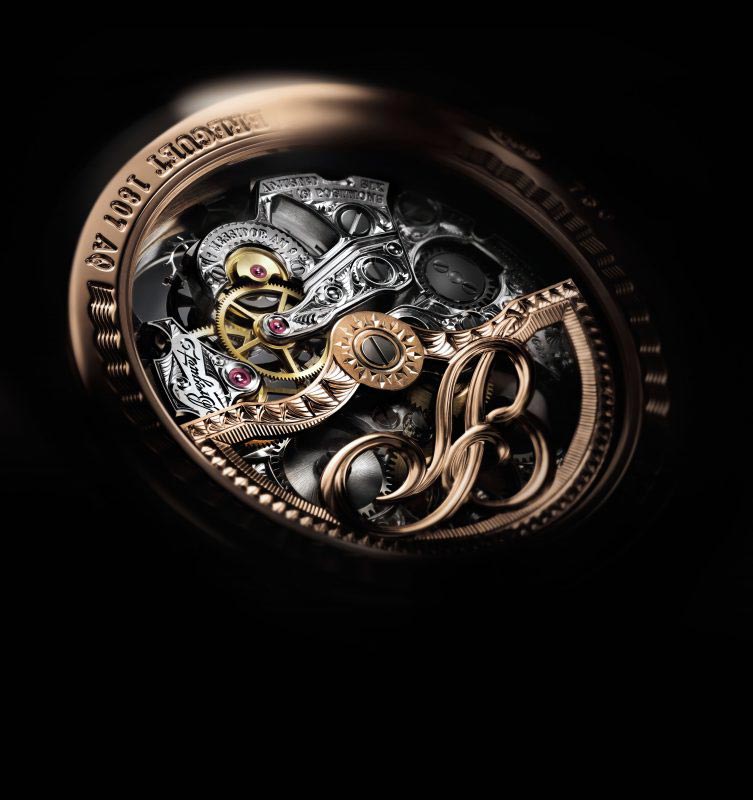
Anglage at the Breguet manufacturer. The decorated rotor on the Classique 5317
Enamelling
Grand feu enamel meaning, “big fire enamel” is a handcrafted technique that few artisans have been able to master in all its subtleties. The enamel paint mixture consists of silica and crushed oxides that are dissolved in water before being applied to a base material (a watch dial base for example) by way of various techniques, such as champlevé, miniature painting, grisaille or plique-à-jour. The real secret to the fabrication, lies in the firing process. The enamel paint added in layers, requires several rounds in the oven. The temperature and duration of the firing is something that only the master knows and depends on the mix of compounds and the techniques used for application. Producing a single traditional hand painted enamelled dial can take up to several weeks.
Experience one of the oldest manufacturers in operation today, and discover the work of Breguet’s artisans respecting centuries old traditions here: https://youtu.be/VAFJwayOIRg